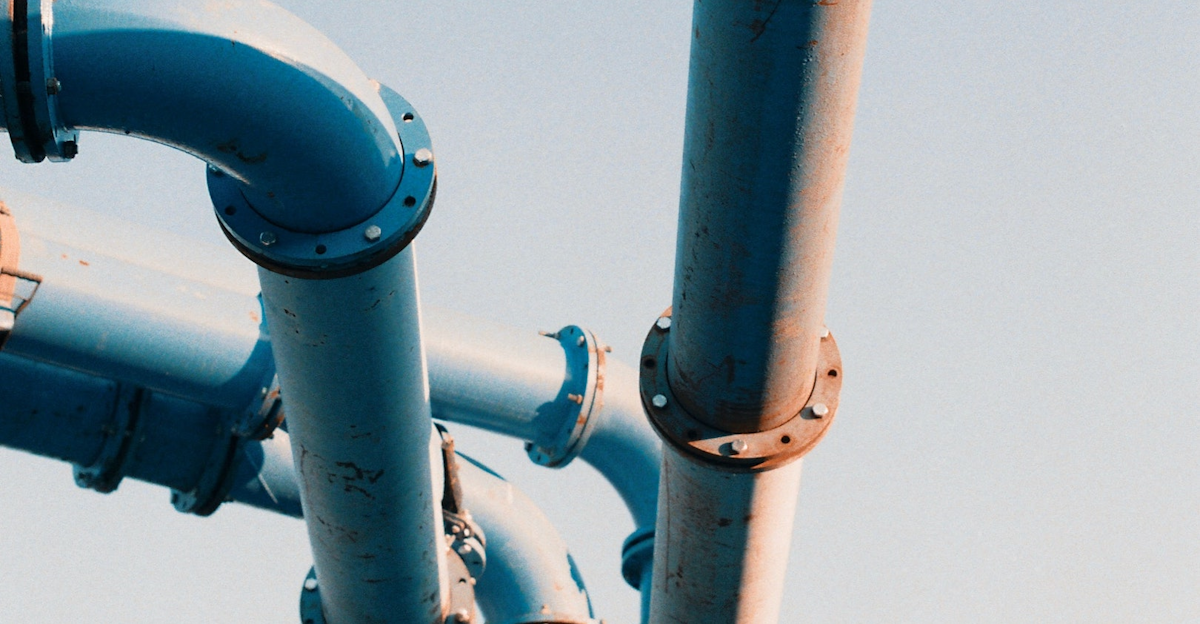
As the largest refined products pipeline system in the country, delivering an estimated 45% of all fuel consumed on the East Coast, the cyberattack forcing operators to shut down the Alpharetta, GA-based Colonial Pipeline has the potential to have extensive repercussions across the nation’s transportation network. How much of an impact the action has on the nations supply depends on the length of the disruption.
The attack was acknowledged Friday May 7. In a statement, the company said, “At this time, our primary focus is the safe and efficient restoration of our service and our efforts to return to normal operation. This process is already underway, and we are working diligently to address this matter and to minimize disruption to our customers and those who rely on Colonial Pipeline.”
Such an attack also spotlights the importance of continually upgrading the nation’s core infrastructure. Unfortunately, the cyberattack against Colonial Pipeline is only a teaser of the future of cyberattacks, explains Grant Geyer, chief product officer at industrial cybersecurity company Claroty.
“As cyber criminals and foreign adversaries seek opportunities for financial gain and power projection, our national critical infrastructure is an easy target. Industrial environments are operating with infrastructure that commonly maintains obsolete technology that can’t be patched, and staff that frequently are not as cyber savvy as they need to be to keep attackers at bay,” says Geyer. “This leads to a situation where cyber security risk levels are below acceptable tolerances, and in some cases organizations are blind to the risk.”
Continues Geyer, “One additional risk factor of pipelines is that they are highly distributed environments, and the tools that are used to enable asset operators’ remote connectivity are optimized for easy access and not for security. This provides attackers opportunities to sneak through cyber defenses as we saw in the water utility attack in Oldsmar, Florida earlier this year.”
Among critical infrastructure sectors, energy is especially at risk, adds Geyer. “Our researchers have found that the energy sector is one of the most highly impacted by industrial control system (ICS) vulnerabilities, and it experienced a 74% increase in ICS vulnerabilities disclosed during the second half (2H) of 2020 compared to 2H 2018. Improving the nation’s critical infrastructure is going to require a public-private sector partnership given the current gaps and potential risk to the US supply chain and national security."
We will continue to update this article as more information surfaces.
The magic formula for digital transformation in manufacturing involves the successful convergence of vision, culture, people, processes, and technology. Vison and culture must be joined at the hip when companies undergo a major metamorphosis like transitioning to a wholly digital environment. It is also crucial for processes to be underpinned by the organizational setup (i.e., employees assigned the right roles, responsibilities, and tools).
It’s not news that B2B and B2C demand is pushing manufacturers and supply chains to create and deliver more complex, customized products. Then there is the pressure of delivering these products within hours or days after the customer has placed the call-out or order. It all adds up to a multilevel exercise that can be made even more complicated by unknowns or unclear data.
Global manufacturing players are pushing forward in leveraging digital technology to bring more structure to this environment. IDC predicts that, by the end of 2021, 90% of global manufacturing supply chains will have invested in the technology and business processes that will bring true resiliency to their operations.
Almost one-quarter of IDC 2020 Supply Chain Survey respondents said their main focus is to improve end-to-end supply chain visibility. This aligns with the perception that a lack of supply chain visibility/flexibility hinders the ability of managers to observe changes and react to them in a timely and effective manner. This challenge has been recognized for years, of course — and it is still among the top three obstacles cited by managers.
Supply Chain Resilience: Challenged by Conditions
It could be a pandemic, a Brexit, or a tanker blocking the Suez — whenever a new crisis arises, the supply chain resiliency of manufacturing organizations comes into sharp focus. Whatever the situation, the supply chain must remain responsive to demand, real and projected.
But a buoyant, hardy supply chain alone does not make a company resilient. Resiliency arises based on all elements of a complex value chain: demand, production, supply. Despite improving intelligence, forecast precision still varies. Accuracy depends on a range of factors, including product type and geography. It is extremely important that forecast precision be fortified by flexibility and internal capabilities.
To handle disruptive dynamics, sales and the supply chain must work together. Digital technology can provide simulation capabilities, and it is essential to have a system that can visualize matches of demand and supply (i.e., inventories and capacities).
Automation and Intelligence
Supply chain managers across industry and product types have a common target: to predict a likely scenario based on demand signals (which, in turn, trigger processes). To accurately detect demand, the availability — and quality — of data are vital.
Organizations are deploying a range of tools and solutions to empower robust integrated business planning process and day-to-day operations. IDC research has found that, in three years, manufacturing organizations will prioritize big data analytics, cloud-based solutions, IoT and B2B collaborative platforms.
The drive for integrated business planning process and supply planning/execution raises the issue of AI and ML. There’s no one-size-fits-all answer. Like it or not, AI-based models are becoming critical to supply chain management.
Planning algorithms are very sensitive to specific use cases. Customized algorithms are needed in different industries. But this effort provides significant value. Pattern recognition algorithms, for example, boost forecast accuracy by processing demand signals — thus predicting patterns.
Reliable and safe infrastructure is the cradle of the supply chain digital brain. For some manufacturing organizations, deploying a nearly real-time digital twin of the supply chain is becoming a reality. IDC predicts that in 2024, half of manufacturers using supply chain orchestration control towers will have integrated supply chain digital twins. This is expected to result in a 10% improvement in innovation delivery and disruption avoidance. Henkel and Bayer, for example, are building digital twins of their supply chains. They are implementing end-to-end visibility, supported by integrated automation and intelligence.
Implications for Technology Users
Building a resilient supply chain requires precise forecasting, the ability to rapidly adapt to short-term situations, supply chain flexibility, and being able to detect problems at an early stage. These capabilities must be captured in processes that rely on decision-making based on data available any time, any place.
Enhanced collaboration inside the company is vital — and I do not mean cooperation in only traditional functions like supply chain, sales, and production. I am talking about IT. The importance of IT continues to rise. IT does not merely provide infrastructure — digital technology actively supports lines of business and improves processes. Supply chain managers must understand that their role has evolved. They are now key enablers of digital transformation.
To make the entire organization resilient in a sustainable way, all technology users must become IT semi-experts. This should be seen as a key new evolution, aimed at overcoming the “mind silos” of traditional supply chain processes and IT infrastructure that waste the potential of digital technology.
But even close collaboration between IT and the supply chain is not enough. Organizations must have real digital leadership. And technology users inside the organization must become, if not experts, then technology influencers who actively demonstrate how digital technology makes supply chain processes increasingly reliable, lean, and precise.
Jan Burian is senior director, head of IDC Manufacturing Insights EMEA and leader of Europe: Future of Operations Practice.
"flow" - Google News
May 06, 2021 at 10:56PM
https://ift.tt/3uyHnGt
Cyberattack on Colonial Pipeline Disrupts Normal Flow - IndustryWeek
"flow" - Google News
https://ift.tt/2Sw6Z5O
https://ift.tt/2zNW3tO
Bagikan Berita Ini
0 Response to "Cyberattack on Colonial Pipeline Disrupts Normal Flow - IndustryWeek"
Post a Comment